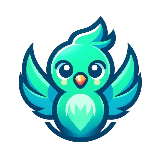
Stress analysis of pipe supported as a propped beam with a udl
- or -
Post a project like this- Posted:
- Proposals: 9
- Remote
- #2581128
- Awarded






Description
• Determine the location and magnitude of the maximum bending stress, shear, torsional, thermal stress and combined stress
• Investigate and quantify different support methods for reducing the maximum tube stresses:
o changing support 1 to a pivot support,
o adding additional support mid-span,
o adding two additional supports at 1/3 and 2/3 span
o reducing the tube ID (increasing the wall thickness)
NOTE: THERMAL STRESS REQUIREMENT ADDED TO THIS PROJECT UPDATE

Bruce T.
100% (1)New Proposal
Login to your account and send a proposal now to get this project.
Log inClarification Board Ask a Question
-
Hello Bruce,
I see you updated your project with more data that would enlarge the problem size and since this is a case study of a failure that happened before and you need to reduce replacement cost, we should develop this model in a FEA model with accurate setup so we can ensure a valid results with the least error percentage.Bruce T.24 Oct 2019Yes, I've introduced thermal stress into the 'project deliverables' to find out if these have any significance. I still need to define the torsional loads, although I suspect that the associated torsional stresses will be negligible.
-
Hi Bruce. This is an interesting project. In your explanatory brief you state that the tubes have to be replaced every 2 years. What is the nature and location of the failure mechanism that makes replacement necessary?
Bruce T.21 Oct 2019A very sensible question and I wish I could give you a straight forward answer. Unfortunately the current operator does not have detailed records of the tube failures. The general verbal consensus is that the tubes have failed at the bottom approximately 1/3 along the tube length. The failure is often a spit in the tube. I suspect that at this point the stress may greater that then material creep rupture strength at the temperature of the tube at this point during high temperature excursions. We will be fitting 16off thermocouples to the tube at the next plant shut down so that we can measure the actual temperature distribution across the tube. This will provide a good indication of the maximum allowable stress that should be applied to different locations of the tube. (The maximum stresses are likely to be at the cold cantilever end of the tube. This is where the allowable stresses will be much higher and therefore not a problem. However as you advance along the length of the tube from the cantiliver, the tube temperature will rapidly rise and the allowable stress will rapidly decrease.) Hence the need for a good understanding of the static stresses within the tube.
I not so much interested in the 'accuaracy' of the stress analysis, but in understanding of what stresses are important, where they are concentrated, what changes can be made to the support mechanism to reduce the stresses. Hand calcs are just as valid as 3D stress analysis models - what matters most is how well the results are discussed, interpreted and presented. Understanding is key.